製造2課の課長を務める山崎は、2005年に入社し製造部門に在籍。2015年2月から2020年3月まで、株式会社東京鋲兼様との合弁子会社である、STBT(Shibasaki Tokyo Byokane Thailand)に出向し、現地工場の製造技術確立に貢献してきました。製造2課では、切削加工により開けられた交差する穴の内部での、バリ無し仕上げを実現しています。加工技術の特長や、バリ無し仕上げを実現するまでの過程、品質方針などを聞きました。
わずかなバリも許されない高精度部品
製造2課では、自動車のエンジンやブレーキの部品、建機関係の部品を中心に、各種製品の切削加工をおこなっています。その中でも、穴内部に残るバリに対して厳しい要求がある、高圧ポンプ向けの部品の加工において、バリ無しを実現しています。
山崎
「製造している製品のひとつとして、高圧ポンプに使われる「ガイド」があります。製造工程としては、旋盤で外径と縦穴を加工して、縦穴に向かって横穴を開けます。その後が、電解バリ取り機によるバリ取りの工程です。バリ取り後は、1槽、洗浄液入れ替わり式の真空ポンプ付き超音波洗浄機を使用して、異物除去と脱脂をおこなっています。これでエンジンや医療部品に要求される部品清浄度を満足します。洗浄、脱脂をおこなったら冷却、乾燥です。そして、熱処理工程、必要な面への平面研磨をおこなって、検査部門で全数検査をした後に完成します。」
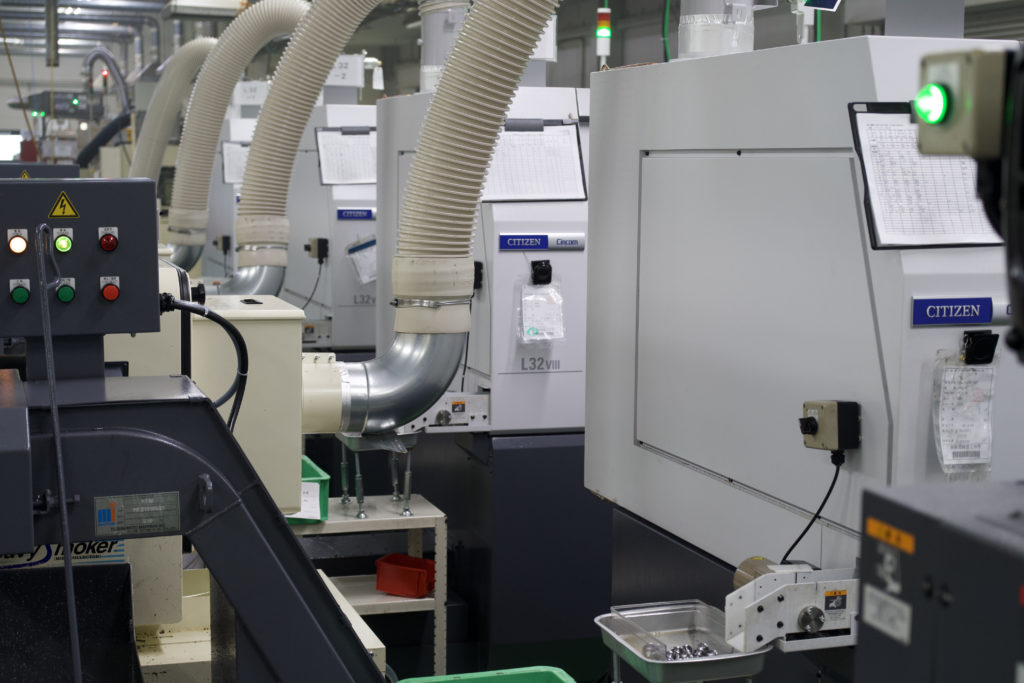
「ガイド」では、交差する縦穴と横穴付近に発生するバリに対して、非常に厳しい要求がありました。飛び出しているバリだけでなく、貼り付くようにできた目立たないバリにおいても、数十ミクロン以上のものは許されず、全て除去しなければ不良品扱いとなってしまいます。
山崎
「この製品を扱うようになった当初は、ブラシを使ってバリ取りをおこなっていました。もちろんブラシでも取れるのですが、取り残しが発生することがあり、品質に差がでていました。何度も使っていると、ブラシが摩耗してバリが残りやすくなるので、品質を維持するために交換が必要です。また、部品1つ、1つにブラシを使うので、量産性という点においても時間がかかります。より確実で効率のよい方法を常に模索していました。」
数ボルト、秒刻みで加工条件を追求
穴の内部にできるバリは、工具や研磨材が入りにくく、除去するのが困難です。そこで考えられたのが電解バリ取り機でした。電解バリ取り機では、加工液を用いて電気化学的に微細なバリも除去します。治具が入れば細長い穴の中でもバリを除去することができて、一度に複数の部品のバリ取りが可能です。これならば、縦穴と横穴の交差部のバリの確実な除去が可能です。ただし、そのためにはクリアーしなくてはならない課題がありました。
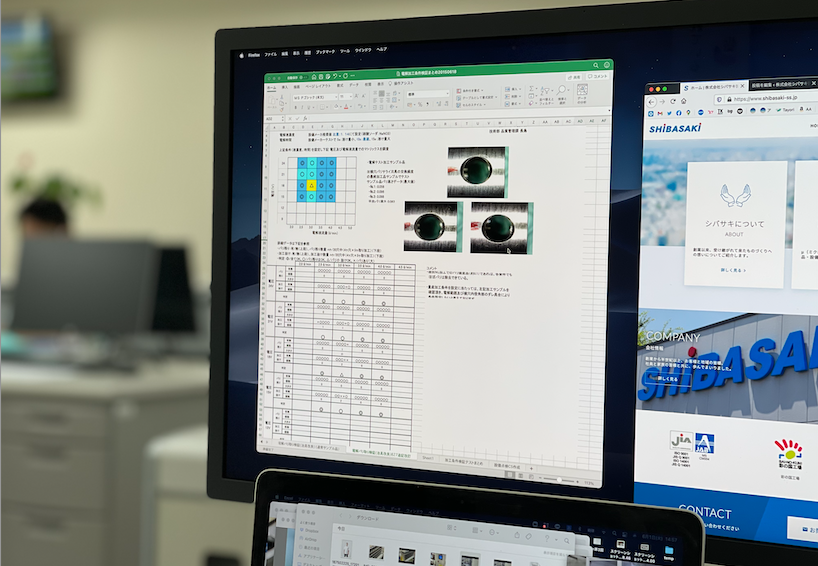
「電解バリ取りにおいては、電圧や加工時間など、色々な要素があります。最適な条件を見つけて設定することが、高精度量産加工における品質安定において必要です。電圧を数ボルト単位で変えて、加工時間も秒刻みで変えて条件を探っていきました。条件出しというのは、初めは時間がかかるものですが、逆に言うと、ノウハウや経験の蓄積になります。」
経験のない加工の条件出しは、あらゆる可能性を考えて、それを1つずつ試していくことになります。経験を積み重ねていくことで、次に別のものを加工する際には狙いどころがわかり、条件出しにかかる時間は短くなります。また、一度得られたノウハウを元に、より高度な加工へ発展させることも可能になります。
山崎
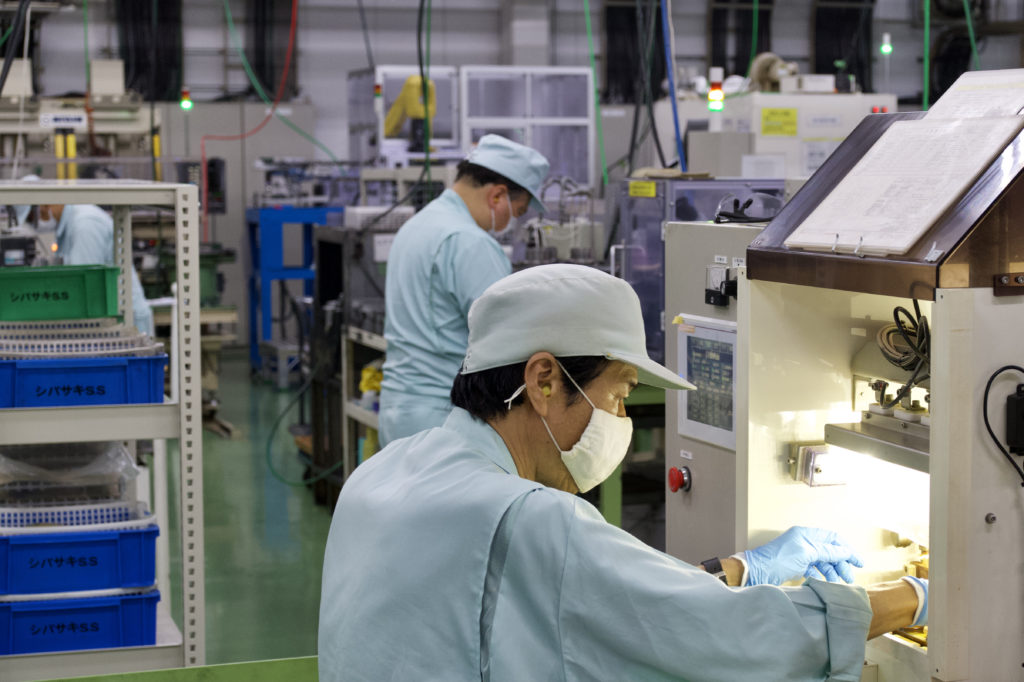
写真:電解バリ取り工程
「やはり、加工条件出しというのは、諦めずに、愚直にやるというのが必要です。ただ、時間をかければいいかというと、そうでもない。量産性や納期という点で最適化を考えると、条件に行き着くまでの時間も、1個あたりを作る時間も、多くはかけられない。最適なところに早く到達するというのは、我々に課せられているブランドミッションではないかと考えています。そのためにも、技術と経験とノウハウの蓄積を繰り返してきました。」
検査部門からのフィードバックを活かす
加工された部品は、検査部門で全数検査をおこない品質を維持しています。お客様に不良品を1つも流さないことを基本に、品質維持のためには、加工時における不良率低下も心掛ける必要があります。
山崎
「お客様に不良品を出さないのが大前提です。不良品が出ていかないように全数検査でそれを止めています。とはいえ、月に何万個も作る部品で、もしかしたら1個や2個、検査を抜けてしまう可能性が無いとは言えません。作る段階から不良品を減らせば、その可能性をより小さくできます。高品質を守るには、製造から検査まで、それぞれの工程を、それぞれが確実におこなうことが大切です。」
高品質の維持には、製造部門と検査部門の連携も重要です。
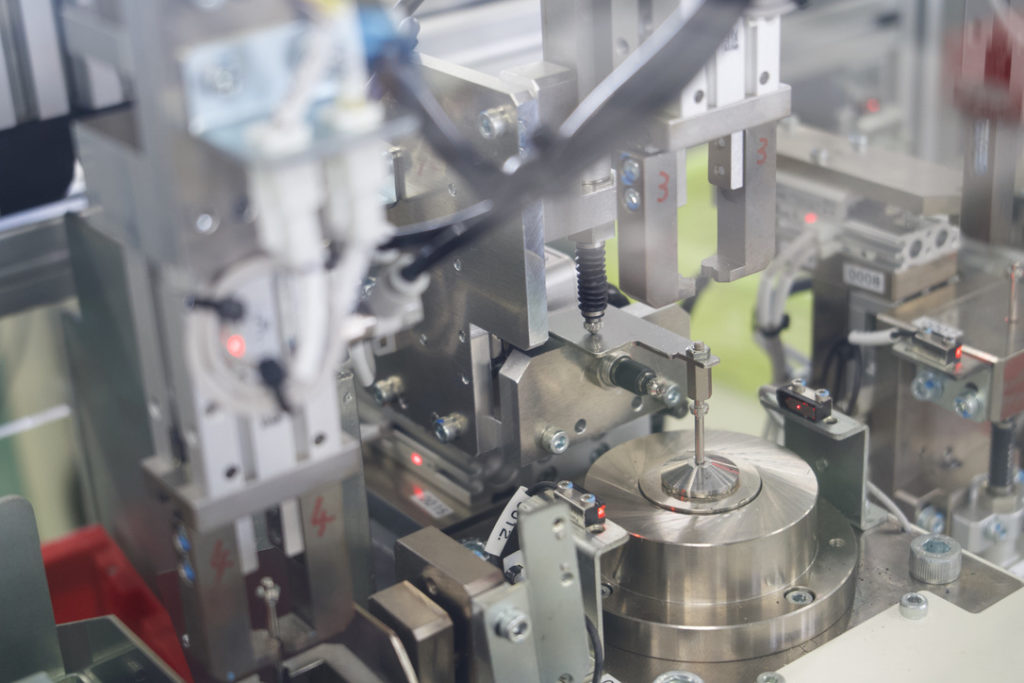
山崎
「問題を的確に改善するために、検査部門から製造部門へのフィードバックは重要です。その情報から、製造部門は元から直さなければいけません。同じ不良を何度も出していると、検査部門も慣れてアクションが鈍くなってしまいます。不良の情報を元に改善する。その結果をフィードバックしてもらう。品質維持のためにも、管理者として、情報交換の活性化を促しています。」
活かせる新分野へも挑戦する
最後に今後の展望について聞きました。
山崎
「現在は、自動車向けの高精度量産部品の比率が多いですが、自動車業界も変化していきます。そこに生まれる新たな需要や、医療、化学、半導体など他の新しい分野でも、当社の技術や製造能力を活用できるところがあれば、製造部門としては是非やっていきたいです。
こんなものはできるかどうか、まずは一度聞いてください。難しい材料や加工精度であっても、条件を出して量産加工にもっていきます。ご相談お待ちしています。」
ー 以上 ー
インタビューとコラムのライティング: 馬場吉成
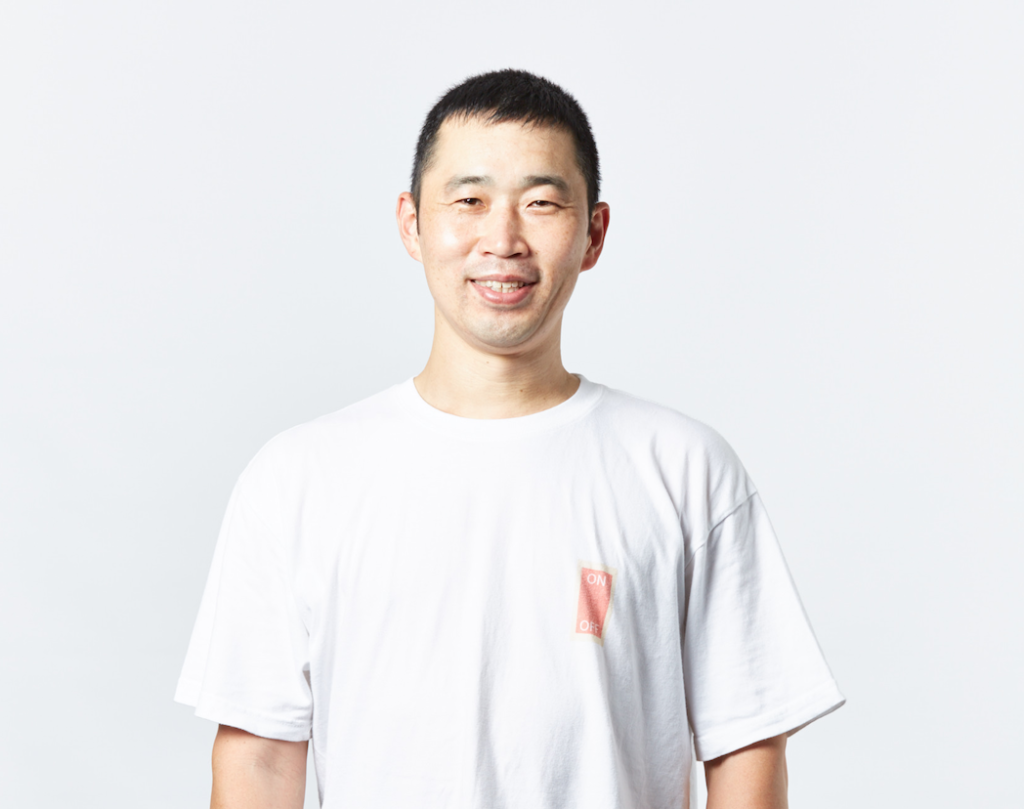
工業製造業系ライター。機械設計の業務を長く経験。元メカエンジニアで製造の現場を直接知るライターとして製造業向け記事、テクノロジー関係の記事を多数執筆。http://by-w.info/